Zipline, a leader in autonomous delivery, has provided an exclusive behind-the-scenes look at their drone delivery operations, showcasing the technology and processes that power their innovative service.
The Heart of Zipline’s Operations
At the core of Zipline’s system are three key components: “Zips,” the fixed-wing drones that serve as the primary aircraft; “Droids,” smaller units that descend from Zips to make deliveries; and docking stations where Zips are charged and loaded.
Lauren Lacey, Lead Mechanical Integration Engineer at Zipline, explains, “Deliveries start at a dock where Zips are charged and loaded… It takes just a few seconds to load and send the order.”
Keller Rinaudo Cliffton, Zipline CEO & Co-founder, emphasizes the efficiency of their system: “These zero emission aircraft are 10 times faster and significantly less expensive than traditional delivery that uses a 4,000lb gas combustion car.”
Rigorous Testing for Safety and Reliability
Zipline’s commitment to safety is evident in their extensive testing procedures. The company conducts thousands of daily tests on each component, runs thermal chamber tests from -50 to 170°F, performs full flight testing in various weather conditions, and runs millions of simulations for potential scenarios.
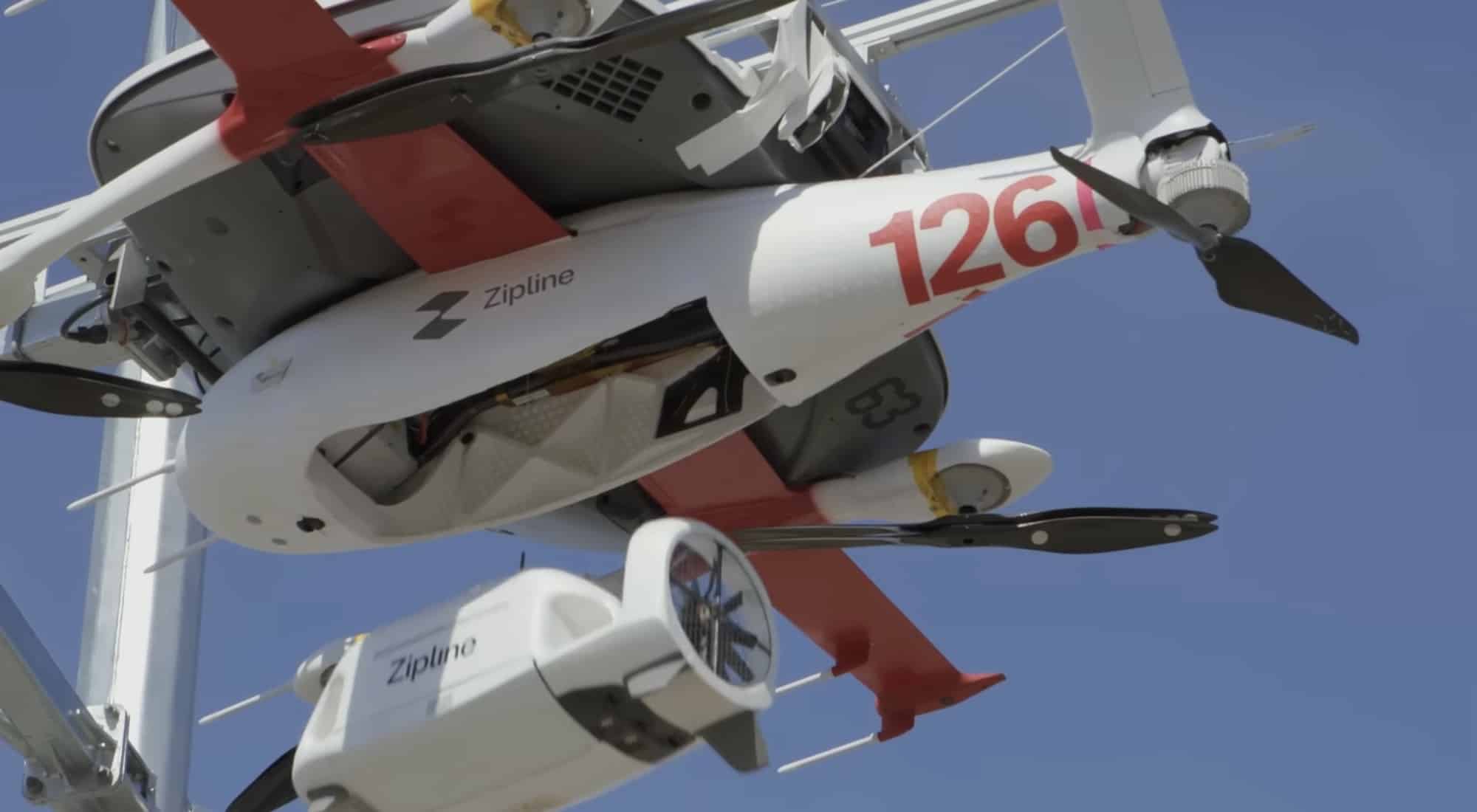
Keenan Wyrobek, Zipline CTO & Co-founder, underscores this dedication: “We push our ZIP steps way past their limits so we know where their limits are.”
Inside the Aviary: Zipline’s Headquarters
Donovan Bass, Head of Product Management for Zipline’s Customer Platform, offers a tour of the company’s South San Francisco headquarters, known as the Aviary. This facility brings together experts from various fields, including aviation, autonomy, mechanical engineering, and customer experience design.
The Aviary features Droid delivery testing areas, prototype docking stations, and loading portal demonstrations, providing a comprehensive look at Zipline’s operations.
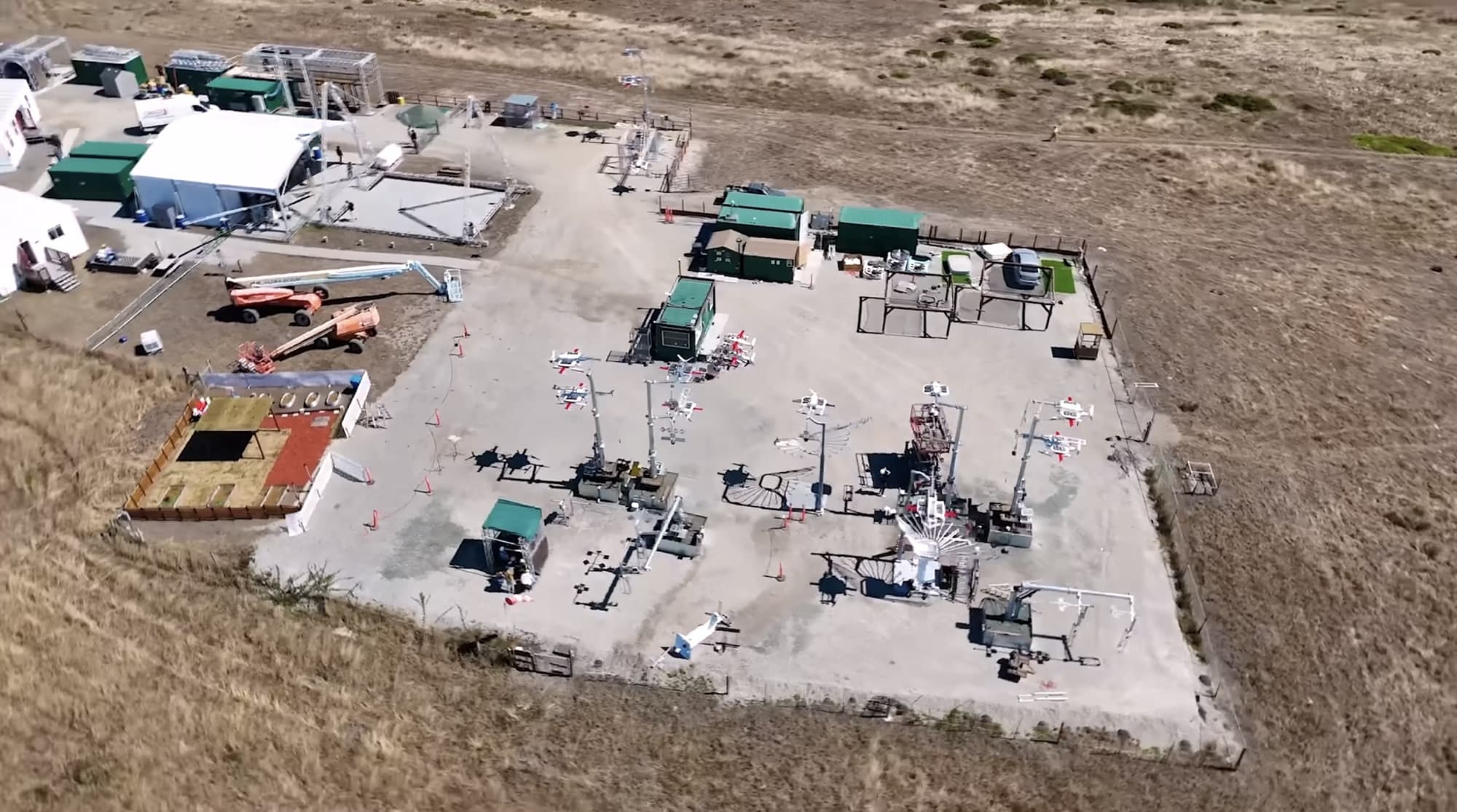
Manufacturing in the USA
Kevin LeLaurin, Head of Material Planning & Manufacturing Operations, reveals that Zipline manufactures its platform in South San Francisco. “By the end of 2025, we expect to produce a zip every hour on the hour at full capacity,” he states.
The manufacturing process includes 12 manufacturing lines tracking thousands of components daily, end-of-line tests for all manufactured products, and custom-built fixtures and testers for quality control.
The Future of Delivery
Zipline’s vision for the future of delivery is ambitious. They aim to make delivery “feel like the internet – instantaneous and universally accessible.” The company believes their service will reduce traffic, improve air quality, and provide faster access to essentials like food and medicine.
DroneXL’s Take
This behind-the-scenes look at Zipline’s operations provides valuable insight into the complexity and potential of drone delivery systems. The company’s focus on safety, efficiency, and innovation is clear.
As drone delivery continues to evolve, Zipline’s approach could serve as a model for the industry. Their emphasis on U.S.-based manufacturing and rigorous testing may also help address regulatory concerns and build public TRUST in drone delivery technology.
What aspects of Zipline’s operations impressed you the most? Do you think their approach will help accelerate the adoption of drone delivery? Share your thoughts in the comments below!
Photos courtesy of Zipline.
Discover more from DroneXL.co
Subscribe to get the latest posts sent to your email.
+ There are no comments
Add yours